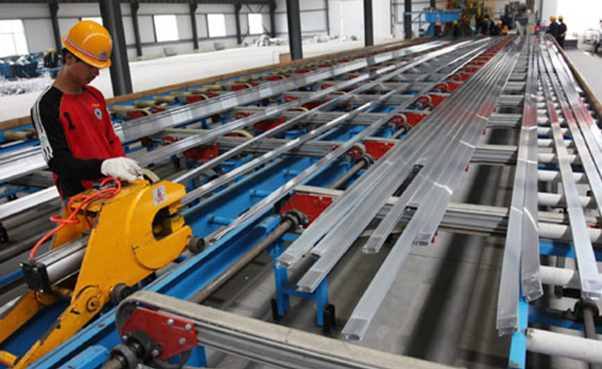
After being quenched, the strength and hardness of the aluminum alloy are not so high, and the plasticity is very good; but after a few days of storage, the strength and hardness will increase significantly, while the plasticity will decrease significantly. The phenomenon that the mechanical properties of aluminum alloys are significantly improved with time after quenching is called age hardening, and this process is called aging.
Aluminum has no allotropic transformation, and there is no eutectoid transformation near the aluminum end, only the solid solubility curve with temperature. When the aluminum alloy is solution-treated, the supersaturated α solid solution at high temperature is left intact to room temperature. However, this supersaturated solid solution is in an unbalanced state at room temperature, and tends to become stable due to desolventization and precipitation of strengthening phases. As time goes by, the strengthening phase gradually desolves to increase the strength and hardness of the alloy, which is the so-called age hardening. There are two ways of aging: natural aging and artificial aging.
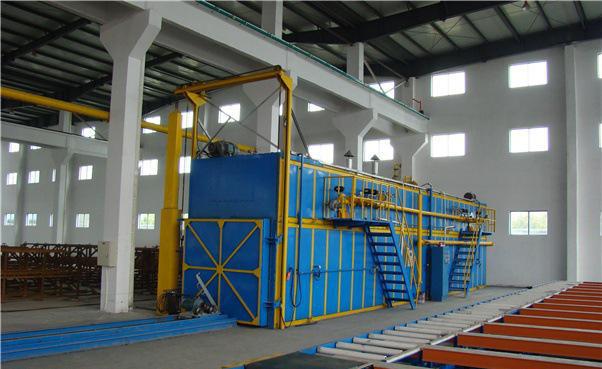
The aging temperature has a great influence on the aging speed. The higher the aging temperature, the faster the aging speed, but the higher the temperature, the lower the maximum strength obtained by the aging. When the aging temperature exceeds 150°C, after the strengthening reaches the maximum value, the effect will decrease if the aging continues, and the alloy begins to soften. The higher the temperature, the earlier the softening time and the faster the softening speed. When the aging temperature drops below room temperature, the aging speed is very slow. At -50°C, the properties of the quenched solid solution will not change significantly even after a long period of aging. According to this phenomenon, aging can be suppressed by lowering the temperature.
Among various age-hardenable alloys, duralumin alloys are generally subjected to natural ageing for no less than 4 days. The wrought aluminum alloy is generally artificially aged, the aging temperature is 150~180℃, and the time is 6~10h. Super-duralumin usually adopts artificial aging, the aging temperature is 120~140℃, and the time is 16~24h. Workpieces that must be artificially aged after quenching should be aged in time, with an interval not exceeding 4h.
The aged aluminum alloy will also produce stress during the cutting process. For workpieces with high precision requirements, stress relief annealing is also required. The stress relief annealing temperature of the aluminum alloy after artificial aging should be 20-40 ℃ lower than the aging temperature after quenching, and the time is 2 to 4 hours. For the duralumin after natural aging, the stress relief annealing temperature should be 80~100℃ and the time should be 2h.
When performing solid solution treatment before aging treatment, the heating temperature must be strictly controlled so that the solute atoms can be dissolved into the solid solution to the maximum extent without causing the alloy to melt. Many aluminum alloy solution treatment heating temperature allowable deviation is only about 5 ℃. For artificial aging treatment, the heating temperature and holding time must be strictly controlled to obtain an ideal strengthening effect. In production, staged aging is sometimes used, that is, it is held at room temperature or a temperature slightly higher than room temperature for a period of time, and then at a higher temperature for a period of time. This can sometimes get better results.